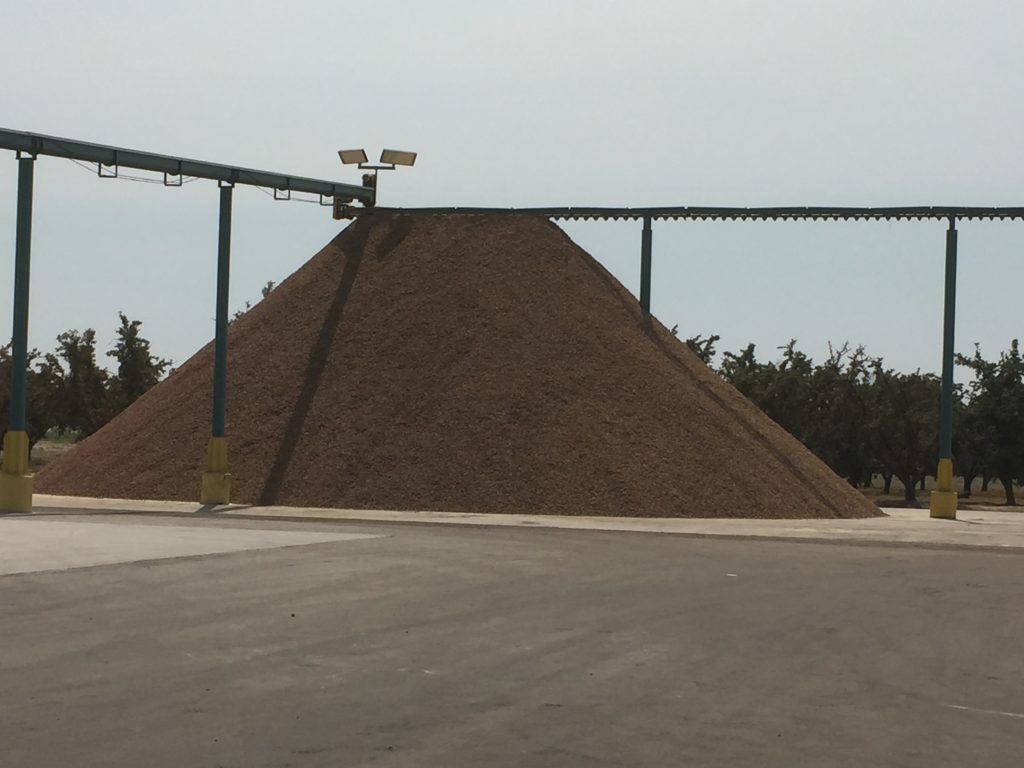
Dennis Pollock, Contributing Writer
Two developments are helping drive the research. The loss of cogeneration facilities in California is making it harder and more expensive to find homes for the wood materials. And the value of hulls has significantly declined as the demands from the California dairy industry are decreasing while almond hull production is increasing.
The almond industry is stepping up research efforts to find alternate uses for almond byproducts that could bring added value going well beyond the value for the nuts.
Almond hulls may be used to produce food grade sugars that could replace high fructose corn syrup. Shells could become a soil conditioner, or could find their way into plastics or even into baby diapers as an absorbent.
Huge machines could recycle whole trees with favorable impacts on soil health.
Two developments are helping drive the research. The loss of cogeneration facilities in California is making it harder and more expensive to find homes for the wood materials. And the value of hulls has significantly declined as the demands from the California dairy industry are decreasing while almond hull production is increasing.
“Three years ago growers were getting $150 a ton for hulls which were fed to cows,” says Bill Ort, bioproducts research leader with the U.S. Department of Agriculture in Albany, Calif. “They were trucked to Harris farms, and the cows were happy.
“But now, the dairy and meat industry are down, and the amount of almonds is up 5 to 10 percent a year. The trees are there; the cows are not there.”
In an address to the Almond Board of California (ABC), Orts said almond biomass in California amounts to 2.4 million tons a year. Eighteen percent is trees, 53 percent is hulls, shells are 22 percent, and the rest is prunings and twigs.
Orts says hulls could compete with sugar beets in the production of sugars, and the Nonpareil variety, the most widely planted, is highest in “free sugars.” He says equipment used by the sugar beet industry could be used on the hulls and would be “cost effective.”
That’s not the case with ethanol production. The grower would have a large cost reduction per ton, he says, and ethanol plants cost millions of dollars to build.
“It would be a big gamble,” says Orts…..[Read More]